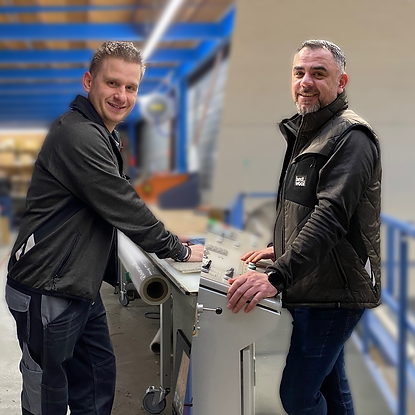
It’s the first impressions that count
Quality starts with our business card!
One works at the beginning, the other at the end of the logistics chain. Jorg Blijs creates the samples that give customers a good impression of Best Wool products. Mehmet Onal and his team are responsible for a perfect delivery of the carpets and rugs. They are clear about their connectedness: ‘Best Wool delivers quality from the first impressions to delivery.’
Anyone who walks with Jorg Blijs and Mehmet Onal through their respective workplaces at Best Wool is touched by the pride that both craftsmen exude. Jorg has been working there for more than seven years and Mehmet has been with the company for more than two decades now. They have experienced the growth of Best Wool and they are proud of that growth. ‘I grew with the company,’ says Mehmet. ‘I started as a warehouse employee and now I am a foreman. Why has Best Wool grown so much? It’s not that difficult – it’s because we have always put the quality of our products and service to customers first. That is in the DNA of everyone who works here.’
Lots of in-house craftsmanship
Jorg underlines the words of his colleague. ‘That is also the beauty of our work,’ he says. ‘For example, we pay a lot of attention to making beautifully finished samples. That is our business card, and we realize that. We already show our customer focus when making the samples. Of course we have standard samples, but if the customer wants a different specification, we are happy to produce it –any size, any shape, and always with the finish that the customer prefers. That also makes it fun and challenging for us. Complex? Sometimes, but we have so much craftsmanship here that it is never a problem. We like to show what we can make.’ Mehmet: ‘It also makes you proud as an employee. Our products are sold all over the world. We do everything we can to maintain our good name.’
Service is key
Mehmet and his team are responsible for the logistics process. For example, if Jorg has to make new samples, he always ends up consulting Mehmet via the Customer Service department. He ensures that the required materials are removed from stock so that Jorg can get to work with his team. ‘Carpets and rugs pass through our hands several times during the process,’ says Mehmet. ‘We are actually the link between production, sales, and our customers. Of course we play an important role, but that applies to all departments. Best Wool delivers top quality, where service to our customers is key. If you want to deliver top quality, you have to focus on that quality throughout the entire company, and monitor and control it continuously.’
Distinctive product
Meanwhile, Jorg shows the samples that are currently being worked on. ‘This one has a blind finish, but we also make them with a woollen serged edging,’ he says. ‘And small, medium, large, round, organic. We even make hearts out of it if the customer wishes. Ultimately, a sample is an important tool when choosing the colour and design that matches the desired rug or carpet. Our product is distinctive from the start: from development to the machine, the first roll, and finally the sample. We are therefore often one of the first to see the product development when samples have to be created. And beautiful samples contribute to our business card, because the first impressions count. Fortunately, everything that follows that sample is also of absolute top quality. So we are more than satisfied, which is evident, right?’
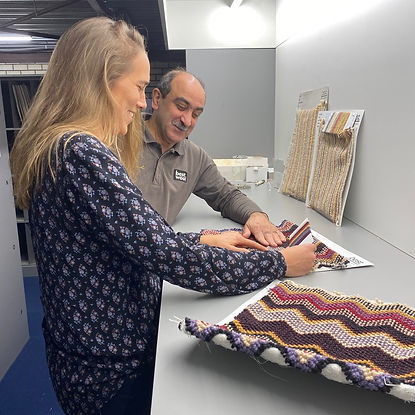.jpg)
Frontrunner in quality and sustainability
Best Wool wants to produce the most beautiful, the best, and the most sustainable carpet
A high-quality product that is sustainable in all respects. It is often said, but is it really true? At Best Wool they don’t like empty promises – say what you do and do what you say. With a good dose of humour, big words such as quality and sustainability are given concrete substance. ‘We challenge ourselves to do better and better,’ says Trudy Backus, Quality & Sustainability Manager of Best Wool.
Best Wool is known for its craftsmanship and keen eye for detail. With the best wool as basic material, the best is extracted from our people and our machines to ensure that the most beautiful products are made. ‘We keep raising the bar for ourselves,’ says Trudy.
Trudy studied technical business administration and – before she came to Best Wool four years ago – she had already gained a lot of experience in the textile industry. She knows what she is talking about. ‘At Best Wool we extend our knowledge in the field of quality. Where exactly does our wool come from, what products do our spinners use to process the wool into yarn, what quality requirements are set for production? In principle, we want to know everything and to be able to check everything. Why? We want to deliver a good end product and we feel responsible for it. We take that responsibility very seriously, so we want to be able to trace everything towards a passport for each product, which specifies exactly what the customer is getting. And of course the data must be correct. That is my job, I feel responsible for that.’
Recycling
Another element that is gaining more and more emphasis is circularity. Many suppliers and manufacturers refer to something as quickly recyclable. For Trudy, it is a term that has too little meaning. ‘Recyclable is nice, but of course it is about whether you actually recycle it. Sustainability encompasses a broad area where the reuse of materials plays an important role, but it also concerns animal welfare, for example. We want to lead the way in the broad field of sustainability. Our customers want that too, by the way. They challenge us. At Best Wool we are increasingly going into depth in this area. We use innovative technologies to extend the life of the materials used, ultimately to return the wool to nature. Everything is done with the aim of being able to roll out a completely transparent and circular concept. Waste? Ultimately, we want to get rid of that completely.’
Artwork
Ali Kharallah nods in agreement with his colleague’s enthusiastic story. As Technical Production Coordinator, Ali is responsible for implementing the high quality requirements on the work floor. Ali has seen the company grow and is proud that he still recognizes the same red line in the production process. ‘I’ve been working here for 30 years,’ he says. ‘When I started, there were about six or seven people in the canteen. You can’t imagine that now. In my first years here, the emphasis had always been on quality. We don’t make carpets, we make artwork. That’s how people feel about it. We are proud of what we make.’
Our customers want consistent quality
Where Trudy deals with product specifications, certifications, regulations, processes, and procedures at the front end of the production process, Ali is responsible for ensuring that the requirements set are translated into the end product. Ali manages the operators and shares his extensive knowledge with his colleagues.
‘I have also worked in the metal industry, but this material has different requirements. Natural fibres are different every time. The customer wants consistent quality, but the basic material is never quite the same. You also have to deal with requirements in the field of fire retardancy and you want every carpet to be at that distinctive, high-quality level. It requires a lot of craftsmanship, but luckily we have that in-house here. We have a good reputation worldwide for a reason.’
High standards
This worldwide reputation in the field of quality and innovation is also a reason for Trudy to continuously look for improvements. ‘We set high standards. Of course we are also audited by external parties to see if we meet the standards, but we want more than that. We also want to take more control over quality ourselves. We are building our own laboratory to optimally monitor all processes and to investigate for ourselves which applications a development is suitable for. Soon only the yarn will arrive, we will do the rest ourselves. We want to keep learning and improving.’ Ali: ‘Quality is mainly in the connection. We draw up the correct specifications for each product. These then enter our ERP system, and we get to work. Quality and durability have full focus here. We want to make the most beautiful, the best, and the most durable carpet. That was already the case when I started here 30 years ago. Fortunately, that is still the case.’

How are designs created at Best Wool?
‘Together we create something special we can be proud of’
Best Wool celebrates its 40th anniversary this year. This also means that we have been making new designs for already four decades. A complicated process? Colourist Marion Cooijmans and Production Manager Frank van Amelsfoort don't feel it’s like that. They consider it as a challenging process and appreciate that Best Wool always opts for the best quality.
Those who compare carpets and rugs often do not realize that behind a certain colour combination or technique, a complete story is hidden, because a certain design doesn’t just happen.
Marion knows that better than anyone. ‘What I appreciate about Best Wool is that they always go for the best quality. Moreover, I find it very challenging to work with a natural product such as wool, which is never exactly the same.’
Creative process
Marion keeps a close eye on developments within the industry. The creative process of a colourist is ongoing. ‘It is up to me to follow the trends and advise our product development. In this way I check whether designs and colours match with the market demands.’ Marion – who can be very happy with a beautiful colour – is inspired by all kinds of things – lectures, books, fairs and trend watchers. ‘Then I’ll get to work. There is always a story behind a design. It is not only about a colour or technique, but about what we add to an interior. What influence does a carpet or rug have on the atmosphere and experience in your bedroom or living room?’
Room to experiment
When a certain design and colour scheme is chosen, it must be technically worked out on the machine. Frank usually can’t wait to get started. ‘I've been working at Best Wool for four years now,’ he says. ‘After many years of work experience in the industry, I know the company very well. Best Wool stands for quality, innovation and sustainability. Here you get room to experiment, to try something out. We make time for each development process. It doesn’t go “fast, fast”, we really make something special together we can be proud of’. In addition, Frank mentions flexibility in combination with creativity as a strong key value of Best Wool.
Technology and design
Incidentally, new products at Best Wool are not only created by trends and developments within the carpet industry. Due to the high involvement and expertise of our technical staff and the vision of Director of Product Development Frank Conrad, new things are continuously being tried out on the machine and then examined: what can we do with it?
‘A good example is a project in which we combine different tufting techniques. We've been working on that for years now and we’re still not quite there, where we want to be. We continue to fine-tune. To achieve a good result, we have even built a machine on a machine.
If we succeed in creating the dream product, it will give great satisfaction. Then we know that we have created something truly unique.’
Interplay
Marion: ‘The interplay between technology and design makes it so interesting. Within Best Wool, communication lines are very short, and we really do it together. That gives us a good feeling. We are all proud when we have once again devised and made something special.’
From idea to carpet – this is how it works:
1) A new design starts with a good idea. From the technical department – Frank Conrad’s vision, Marion’s creativity or the customer’s wishes.
2) Then Marion gets to work. She translates it into a colour palette and creative collection proposal.
3) The colourist then presents her design to the Best Wool design team. Aspects can still be adjusted or changed.
4) The technical department will work on the design and try to produce it (on a larger scale) on the tufting machine. When the go-ahead is given for production of carpet or rugs, full production can start.
5) The expertise of the commercial department is also called in. They help to bring the new product to the market in a clear, structured and effective way.

Towards developing waste-free carpets
Best Wool and Niaga® partner in building a circular future
Today we are excited to announce the partnership between Best Wool and Niaga®, introducing innovative technology for carpet production that points the way towards a circular future.
Best Wool and Niaga® share the ambition to protect the valuable materials used in woollen carpets and rugs. Their goal is to ensure eventually nothing ends up as waste. Innovative Niaga® technology enables a vastly more energy efficient production process than currently used in conventional carpet manufacturing. What’s more, the Niaga® click-unclick polyester adhesive, that will be used, allows separation of the woollen top layer from its polyester backing at the end of a carpet’s lifecycle. At the same time, Best Wool and Niaga® continue to collaborate closely in optimising the separation and reuse of the wool and polyester.
Cutting back energy usage by 90%
One of the biggest milestones of the partnership between Best Wool and Niaga® is the introduction of an energy efficient production process never seen in carpet manufacturing. This new carpet production technology with Niaga® click-unclick polyester adhesive does not use any gas or water. In addition, it consumes only 10% of the energy required by conventional carpet backing methods, thereby also significantly cutting back on carbon emissions in the production of carpet. This breakthrough in the carpet industry comes at a time when energy costs and the cost of reducing carbon emissions are affecting producers around the world.
Best Wool’s unique 5-meter-wide production line with innovative carpet manufacturing technology will be set up at its production location in Best, the Netherlands. Concurrently, Best Wool and Niaga® are collaborating on the development of technology for separation, recycling and re-use of wool and other materials. The recycling line is expected to be up and running within 3 years. The new production facility, as well as the joint development on material separation technology for wool and polyester has been made possible with the support of the Dutch Ministry of Economic Affairs (RVO).
Retaining each material’s value
Due to the complex combination of materials glued together for eternity, materials used inside a conventional carpet are hard to re-use at the end of life. By joining forces, Best Wool and Niaga® aim to minimise waste and protect the value of materials in woollen carpets and rugs.
The Niaga® click-unclick adhesive allows for separation of the woollen top layer of a carpet from its polyester backing at the end of the carpet’s lifecycle. It’s no longer required to use binders and fillers that make materials inseparable and hinder recycling. Once the material separation technology has been developed, it will become possible to create a stream of wool and a stream of polyester materials that can be repurposed: each material in the best way.
“At Best Wool we consider the creation of a closed loop carpet as a journey which takes time. Designing woollen carpets and rugs for material re-use starts with the end in mind. We’re collaborating closely with Niaga® to see how products need to be designed for circularity. What’s more, ingredient transparency is needed to enable return and reuse of materials” explains Yvar Monasch, CEO of Best Wool.
He adds: “Even with this work requiring more time and effort, we firmly believe that today’s linear economic model is not sustainable. The industry needs frontrunners who show the way and make first steps. We’re proud to be taking these important and essential steps towards a circular future. Because we consider sustainable production methods as the way forward. This is extremely important for the wellbeing of our employees, the surroundings in which we operate and the global climate challenge facing our generation.”
Chris Reutelingsperger, founder of Niaga® comments: “We need to start treating materials as treasure instead of trash. Best Wool shares our vision. Our partnership will show the carpet industry it is possible to make the radical shift that is required to make carpets and rugs in a way that all materials retain their intrinsic qualities, so that nothing is wasted in the end.”
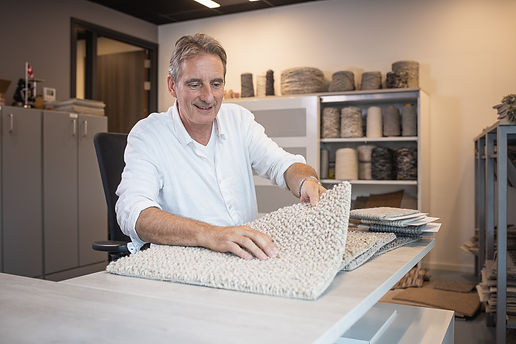
40 Years of Best Wool
‘We continue to innovate, even after 40 years’
A woollen carpet or rug made today is incomparable to one made roughly 40 years ago. And that makes sense. Just like in the fashion industry, the production process for a woollen carpet is subject to the latest trends and developments. Production techniques are changing, and more attention is being paid to design and sustainability. Frank Conrad, Director of Production and Product Development, and his team are responsible for all new product developments at Best Wool. They are the ones who ensure that Best Wool is and remains a leader in the woollen carpet industry – even after 40 years.
Whether sleek and stylish or warm and homely, a vintage look or a modern character: over the years, the number of carpet and rug designs has grown rapidly.
New colours, structures, shapes, and technical applications are constantly being created. ‘That offers a fantastic challenge for us, every single time,’ says Frank. ‘Our company has always been passionate about wool. By being creative with designs and experimenting with our machines, we make the most beautiful and best products. Not a week goes by without us working on new product developments. That's what makes my work here so exciting. I'm never bored.’
Product development
Best Wool was originally known as a carpet manufacturer for third parties, but over the years has also developed its own brand portfolio. The company has grown into an authority in the field of woollen carpets and rugs. Product development plays an important – if not the most important – role in this respect.
Frank and his team look at what is technically possible on the modern tufting machines on which Best Wool makes its high-quality products. ‘We really are pushing the boundaries.’
The designs are made and the colours chosen based on the available technical capabilities, which is also how new techniques and developments arise. ‘We regularly surprise machine suppliers who didn't think it was possible to get this out of their machine.’
Best Wool has now fine-tuned its development process so that a new product can be launched on the market within six weeks. ‘That’s extremely fast for our sector. But it’s also necessary. While we used to present a collection for the whole year, nowadays we have to continuously innovate,’ explains Frank.
Circularity
Recent years have seen a growing interest in the topic of circularity. This is an excellent development for Best Wool, as the company has been dedicated to sustainability for decades. Frank shares an example: ‘We are now working on a machine that makes the entire production process circular. We ourselves are at the forefront of this technology, which enables us to separate a polyester backing from a second-hand carpet and floor covering using a reversible adhesive. Our aim is to reuse that wool in areas affected by drought. The wool offers a perfect surface for germination, so it can support grass growth for sheep to graze on. This is our way of giving the wool back to nature, as it were, wherever it comes from. We’re closing the loop – from grass to grass.’
Natural product
It is clear that Best Wool is a frontrunner in carpet innovation. Frank is proud of it. ‘What we achieve with our tufting machines is truly unique. Remember that wool is a natural product, which is almost impossible to standardize. Every type of wool is different. Where do the sheep live, what do they eat, what is the weather like there? All these factors play a role and give each type of wool its own character. It's up to us to deal with that.’
How does Best Wool guarantee high quality as standard? ‘That's the chef's secret,’ Frank laughs. ‘It’s in a number of things that are also part of our core values: passion, craftsmanship, and 40 years of expertise in wool. But it’s also related to the good, reliable agreements we make with our suppliers. We have high requirements, we want to deliver the best quality, and we also want to fulfil our ambitions for the future.
Doing so means we can continue to surprise our customers, every day. Because we continue to innovate, even after 40 years.

40 Years of Best Wool: How it started
Does she remember the early years? “Of course, like it was just yesterday!” says Nelleke van Doorn. Although it was 40 years ago, the widow of founder Jan-Carel van Doorn still remembers what the company was like during the early years. “It all started with a small team, one machine, and a rented warehouse.”
After a sip of coffee, she starts on her story. “Jan-Carel was always a hard worker who discovered what he was passionate about early on: the carpet industry. After a number of career moves in Belgium, among other places, he was able to realize his dream in 1982: his own carpet factory. We rented a building with an office and warehouse and established Carpet Factory Best, which wasn’t far from here by the way. The building from back then is still part of the current estate.” What did the production facility look like by then? Nelleke chuckles. "Well, different than now that’s for sure. We started with four employees, a second-hand machine, and donated office furniture. You have to start somewhere.”
The couple found a house nearby. “We lived five minutes from the factory. That was very practical. My husband worked very long days, seven days a week. He didn't come home until dinner was ready. And on Sunday evenings? That is when the entire family went to the factory to help out, so we could start tufting right away on Monday morning.”
International reputation
In the early years, Carpet Factory Best mainly produced for third parties, with a very limited private label collection. “We were active on the Dutch and Belgian markets at that time.” This changed in 1987. Carpet Factory Best participated in the international trade fair in Frankfurt and landed a Swiss customer there. And what a customer indeed! The first order they placed was equal to our annual turnover at that time. Jan-Carel was over the moon. He said, “Well, job done, we can go home! Of course we didn't. But we all celebrated the success together!”
Family business
The number of orders increased over the years, as did the number of domestic and international customers. “The company grew and new machines were added. I still remember Jan-Carel being so proud when we started renting a second building, And I was so proud of him.” Despite this growth, the family character has always been preserved. “It was important to us. None of this would have been possible without our staff.” Jan-Carel therefore took good care of his employees. However, he also expected something in return. “People had to work hard,” Nelleke emphasizes. “If a machine stopped running, he could hear it in the office and immediately went to have a look. He wouldn’t lose any time in checking why a machine wasn’t running.”
The successor
In 1996, Jan-Carel started looking for a successor. That was no small task. “Our children went their own ways and there was no suitable candidate to be found internally either.” Eventually, the successor was discovered at a special place. “Jan-Carel and I attended a classical concert. There we met Yvar Monasch, the son of a good friend of ours. Yvar was an inspired young graduate who had quickly made a career in the piano business. He also organized classical concerts. “Do you see what I see?” said Jan-Carel. “We looked at each other and that’s when we knew: he had to be our successor.”
Yvar was therefore given the opportunity to get to know the company and industry. “We gave him a flexible role, he was allowed to fly all over the world to get to know our suppliers and the markets. He seized that opportunity with both hands.” Where Jan-Carel always viewed the company from a technical perspective, Yvar turned out to be mainly focus on the commercial side of things. “He immediately saw a lot of potential in expansion to other countries.”
The confidence in Yvar was rewarded after three years. He would become the new owner. Although the connection with Yvar was good and the mutual trust was significant, Jan-Carel had a hard time with the takeover. “But it all worked out in the end, when you look at the company as it is today. I can only look at Yvar and Best Wool with admiration. He has turned it into a great company, with a beautiful building and eight tufting machines. And look at how well he treats his staff, just like he promised. Most of the people who worked for us are still with the company today. If only Jan-Carel could see it for a moment. I’m sure he would have been very proud.”
.jpg)
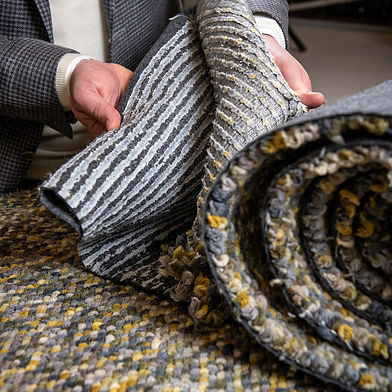
Best Wool empowers a circular future
Inspired by nature’s perfection, we at Best Wool care greatly for people and the environment. Fully aware of our responsibility of preservation of nature’s beauty we continue our efforts in creating comfortable and healthy living environments.
To improve the quality of live is an important part of our mission. Innovation and quality are our driving core values. We feel obliged to protect nature by reducing our footprint and producing woollen carpets and rugs that bring health benefits for end-users.
Best Wool significantly invests in her circular future. As well-known entrepreneurs in our industry we have worked together with Niaga® (Niaga backwards spells “Again”) to develop manufacturing technology which enables decoupling the polyester backing from the wool pile so that both materials can be separately reused. This innovative technology is a vital part of our next generation carpets and rugs, that will be fully circular as soon as we have taken this big step forward.
Best Wool has started engineering a five meter wide production-line to apply the in-house technology. Likewise our offices and current production facilities, this new production line will be powered by solar energy. Furthermore Best Wool will continue its frontrunners position by engineering a decoupling-line that enables recycling and re-use of raw materials. The entire process should be completed within 3 years.
Yvar Monasch, CEO of Best Wool states that this development is a huge step towards a circular future: “We consider clean and sustainable production methods the way forward to operate. This is extremely important for the wellbeing of our employees, the surroundings in which we operate and the global climate challenge facing our generation. It is our ambition to be an authority in the field of circular flooring by 2030”.
The new production facility is an RVO collaboration in which Best Wool joins forces in creating a sustainable strong circular business model. The RVO aims to facilitate entrepreneurship, improve collaborations, strengthen positions and help realise national and international ambitions by funding, networking and expertise in compliance with laws and regulations.
Best Wool has partnered up with Niaga for the implementation of the reversible backing technology and the recycling process for decoupling and re-use of raw materials. Matthys Group is in the lead of engineering and the construction of the new machinery together with Lacom who will supply the laminating technology.
The new production line will be accommodated in the current production facility for which the material storage location will move to a newly built warehouse. Installation of the machinery will follow towards the end of 2022. The new facility will be operational early 2023.
Best Wool has been designing, manufacturing and distributing woollen carpets and rugs since 1982. Genuine and honest natural products for people who appreciate quality and a healthy living environment. Best Wool is known for its creativity, flexibility and innovative design. A leading player and reliable partner in the woollen floor covering industry. The circular wool rug brand Monasch, division of Best Wool, already uses the Niaga® technology .